More Information
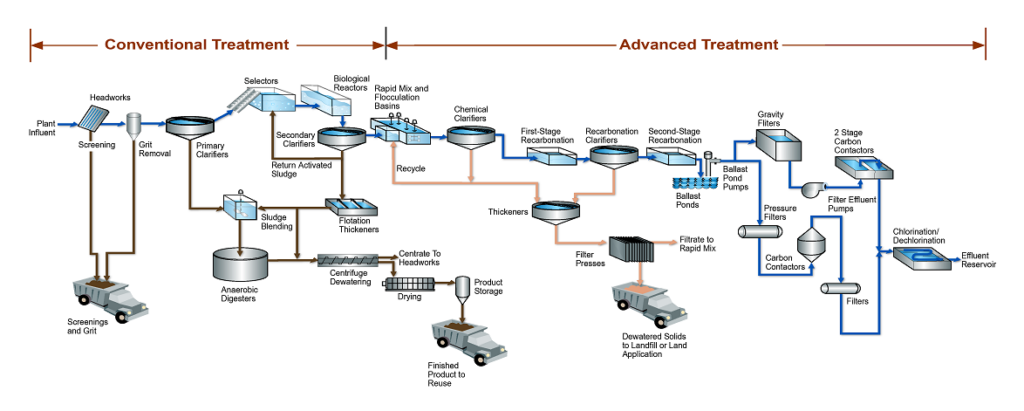
Capacity
- 42 MGD Annual Average Flow
- 54 MGD Peak Month (30-day rolling)
- 128.4 MGD Peak Instantaneous Influent
- 90 Million Gallons On-site Emergency Storage
- 7.5MW Emergency Generator Capacity
Key Permit Requirements
- Chemical Oxygen Demand (COD) < 10 mg/L
- Total Phosphorus (TP) <0.1 mg/l
- Total Suspended Solids (TSS) <1.0 mg/L
- Total Kjeldall Nitrogen (TKN) <1.0 mg/L
- Turbidity <0.5 NTU
Conventional Treatment
Conventional Treatment removes over 90% of incoming pollutants and provides a high-quality effluent for subsequent advanced waste treatment polishing steps.
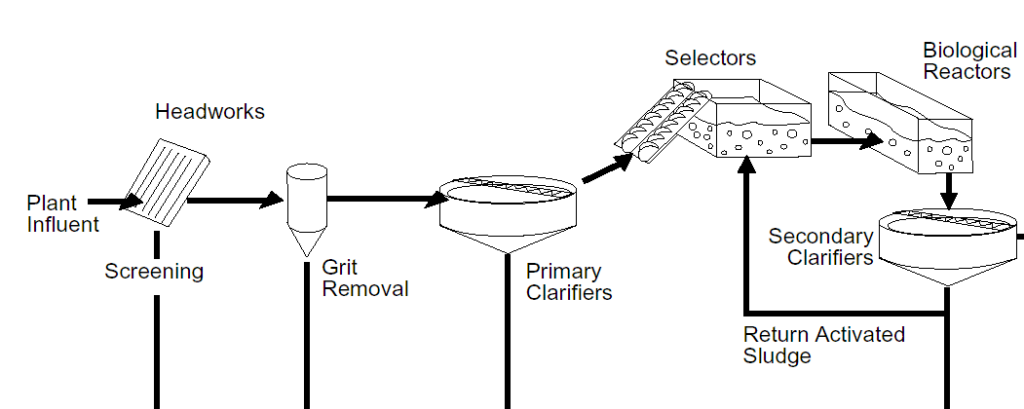
- Mechanically cleaned bar screens (0.5-inch openings)
- Vortex grit chambers, 24-ft diameter
- Circular center-feed primary clarifiers with primary scum collection, 125-ft diameter
- Archimedes screw primary effluent lift pumps
- Aerobic biological selectors
- Activated sludge aeration basins
- Most basins fine-bubble diffusers
- All basins operate in nitrifying mode with active D.O. control
- Four basins have modified Ludzack–Ettinger denitrification process, can achieve 6-10 mg/L nitrate
- Neuros energy-efficient turbo blowers supply air for the bioreactors
- 125-ft diameter circular center-feed secondary clarifiers with draft tubes, slot-valve draft control, and biofoam collection
- Continuous monitoring of secondary effluent TSS, Nitrate, and Ammonia
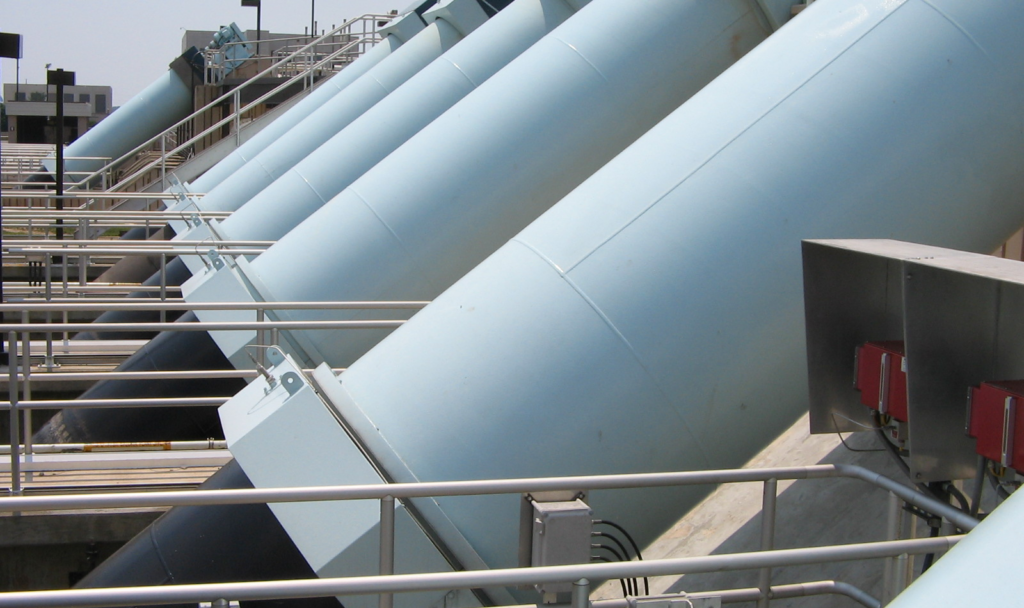
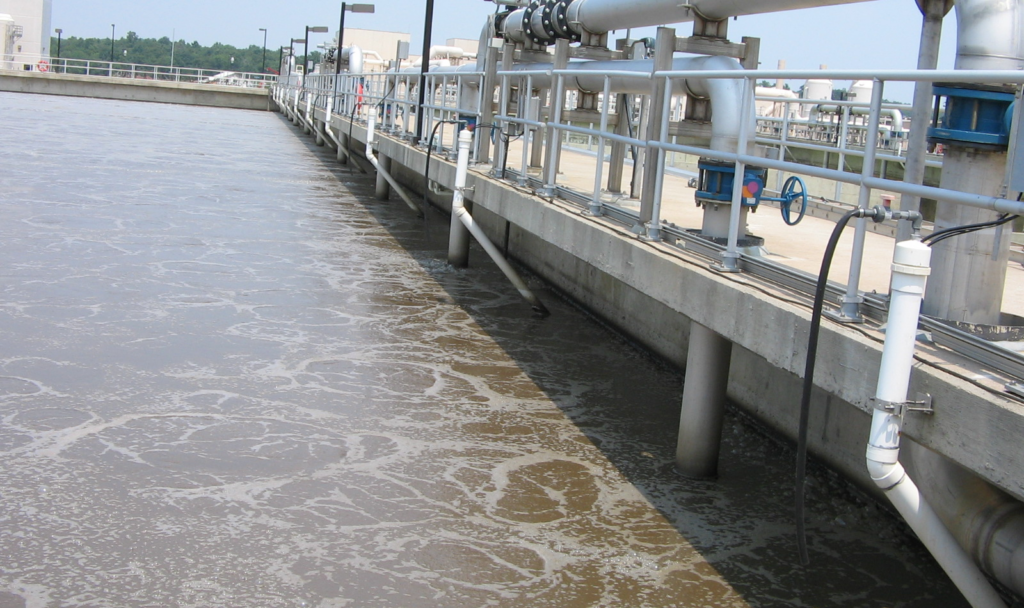
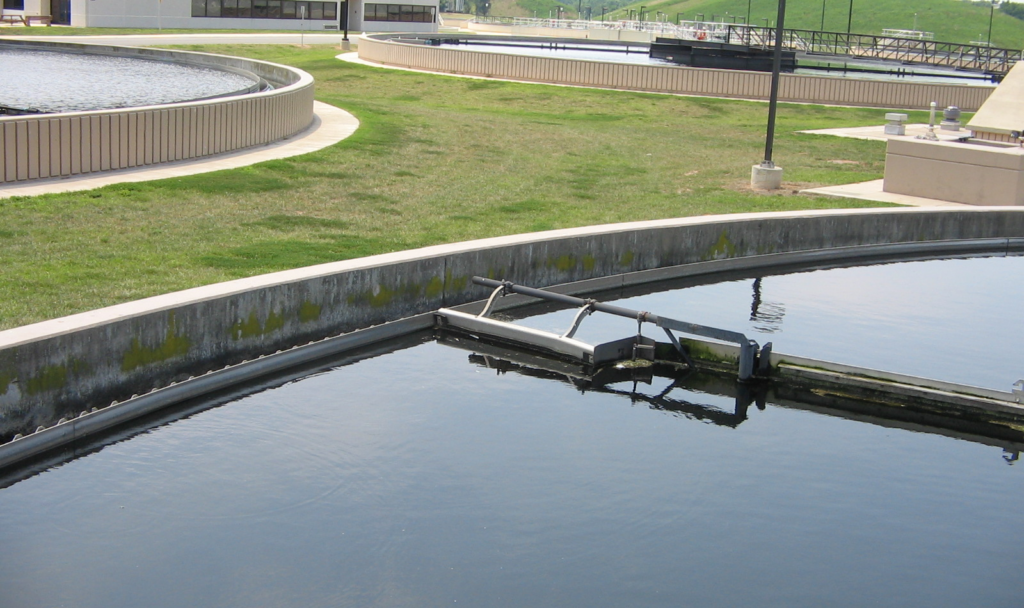
Chemical Advanced Treatment
Process water leaving Conventional Treatment enters the high-lime process, to reduce phosphorus to below 0.10 mg/L. This process also serves as a barrier to viruses, captures organics leaving Conventional Treatment, and precipitates heavy metals.
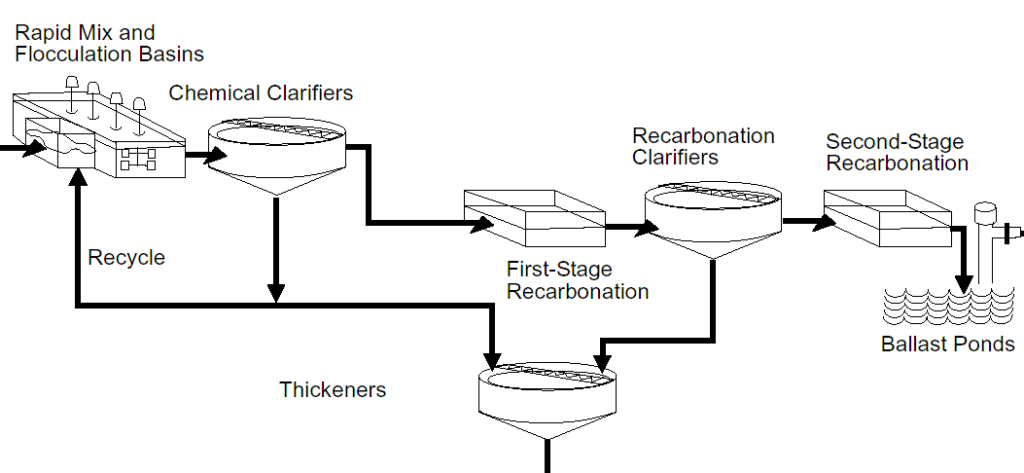
- Silos with total storage for 240 tons of calcium oxide as pebble quicklime
- Detention-type lime slakers with lime aging tanks
- Rapid mix basins for lime slurry addition computer controlled to pH 11
- Declining-rate flocculation basins
- Chemical clarifiers, 125-ft circular
- First stage recarbonation lowers pH to 10. Second stage lowers pH to 7 (neutral).
- Both stages use coarse-bubble diffusers and introduce exhaust stack gas containing waste carbon dioxide from digester boilers, carbon furnace, and pelletizer furnaces, capturing greenhouse gas from emissions.
- Recarbonation clarifiers between first and second stages to collect precipitated calcium carbonate
- Gravity thickeners to concentrate chemical and recarbonation sludge
- Recessed chamber plate and frame filter presses to dewater sludge
- On-site 2 million cubic yard captive landfill for dewatered lime solids
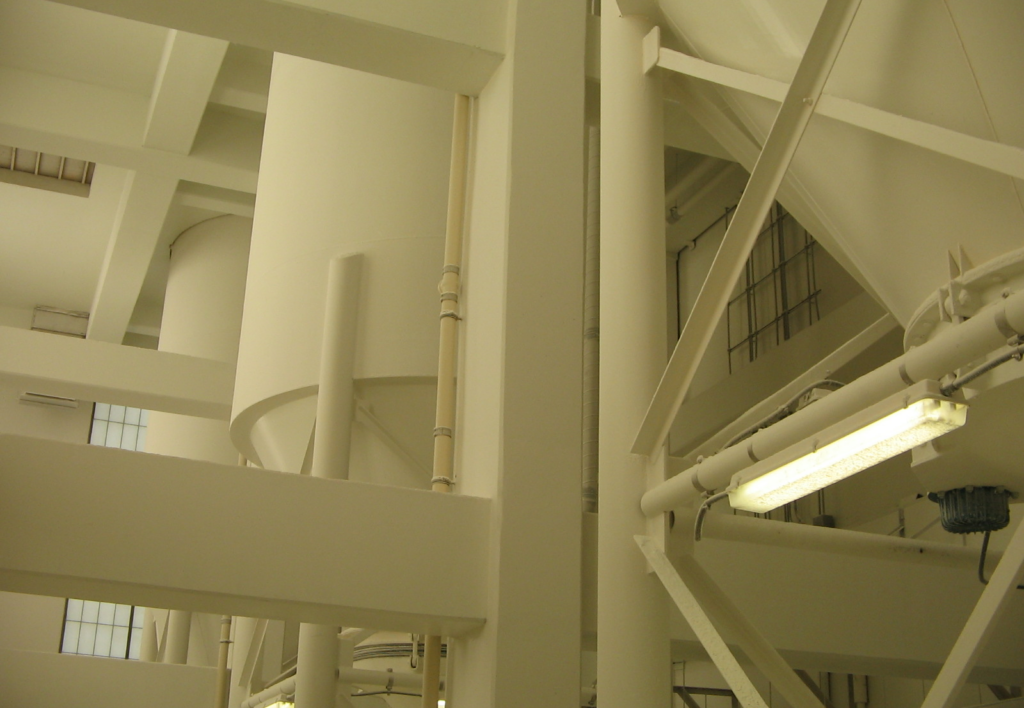
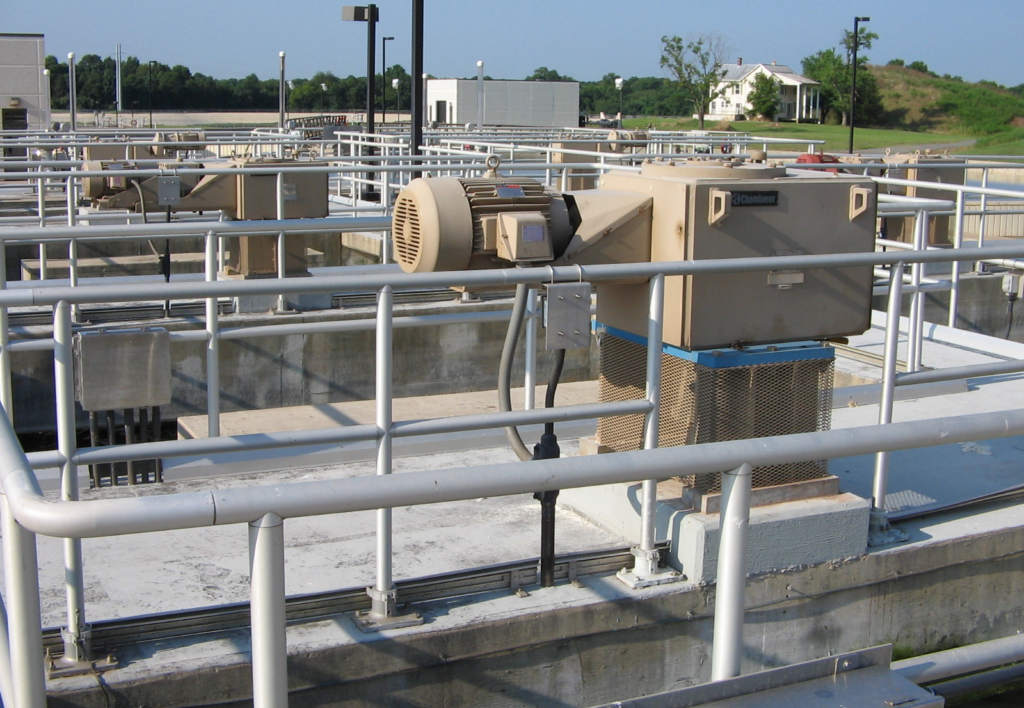
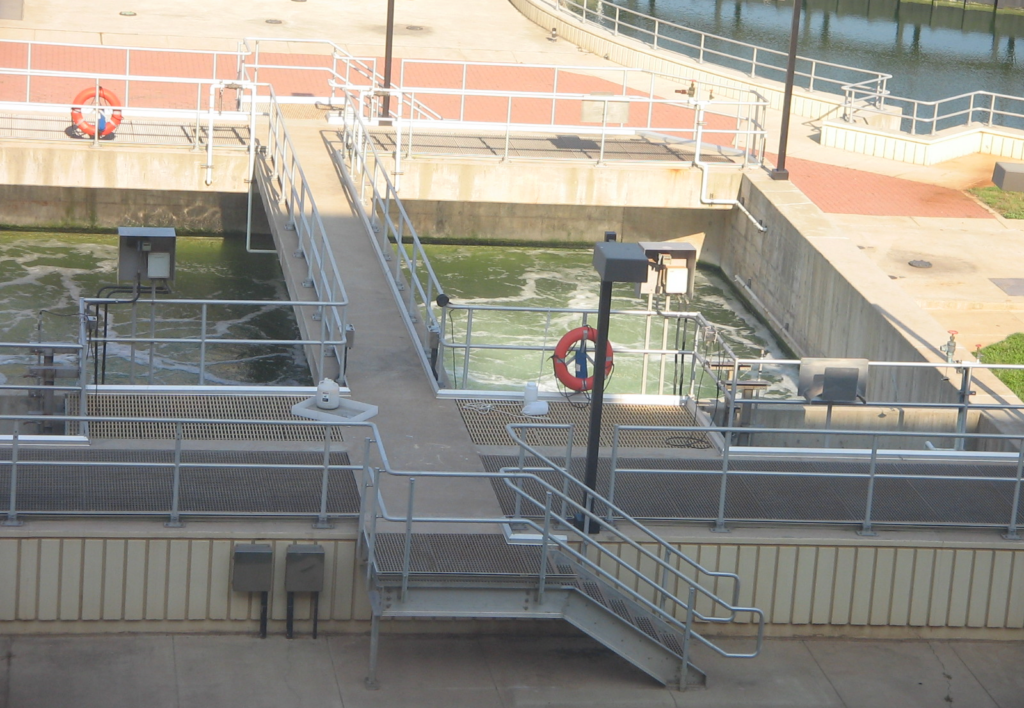
Physical Advanced Treatment
Process water leaving Chemical Advanced Treatment enters a Physical Advanced Treatment process. The UOSA permit requires TSS below 1 mg/L and COD below 10 mg/L. To meet these stringent levels, multimedia depth filtration and activated carbon are used.
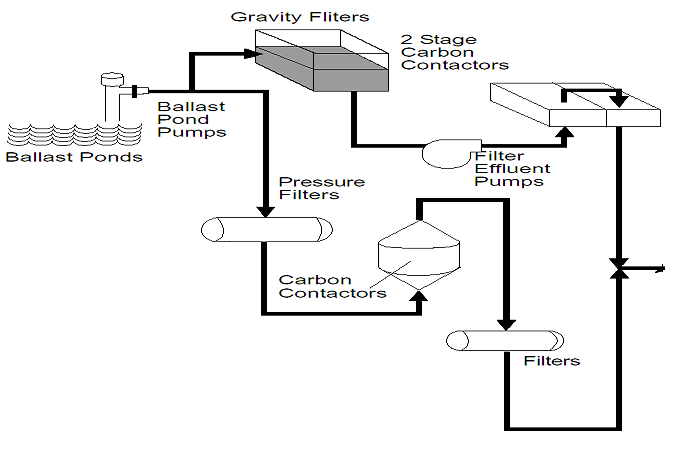
UOSA has two process trains, one with pressure filtration/carbon and one with gravity. The gravity system is as follows:
- Six 100-hp vertical turbine pumps transfer effluent from Chemical Advanced Treatment to filters
- Alum is used as a filter aid
- Ten multimedia filters with 36-inch bed of anthracite, silica, and garnet
- Continuous online turbidity analyzers
- High-rate backwash with air scour
- Intermediate filter effluent pump station pumps filter effluent to carbon
- Eight upflow/downflow carbon contactors with 2 million pounds of activated carbon
- Carbon transfer facilities to facilitate carbon regeneration or replacement
The pressure process train is similar.
Activated carbon is regenerated onsite with a multi-hearth furnace
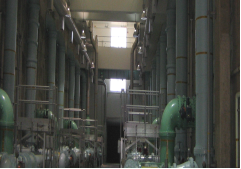
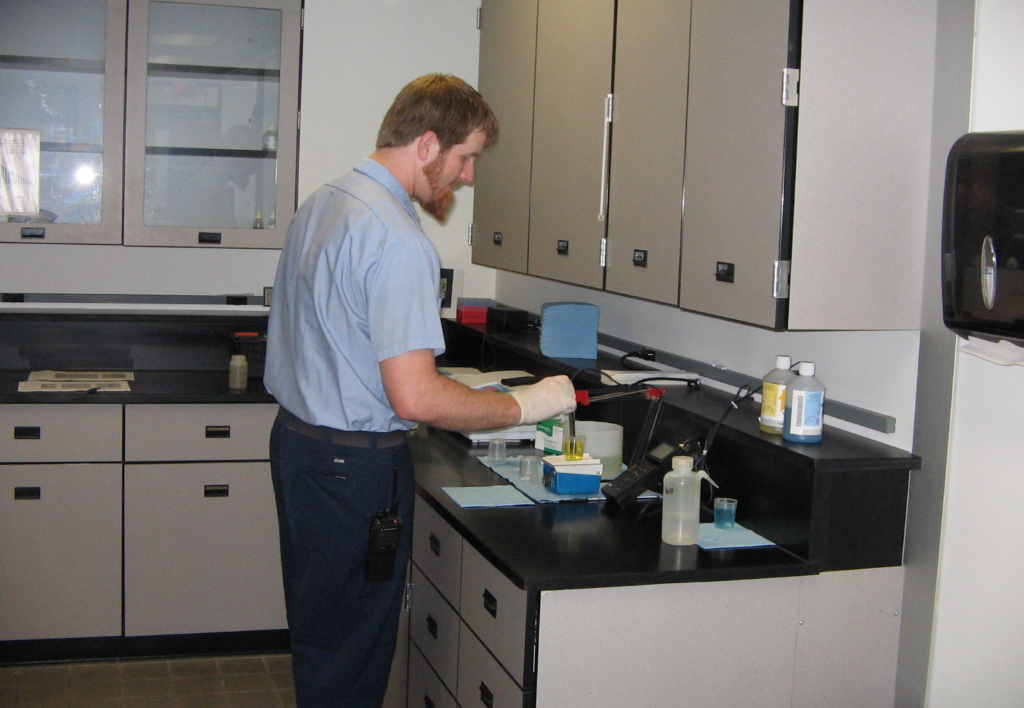
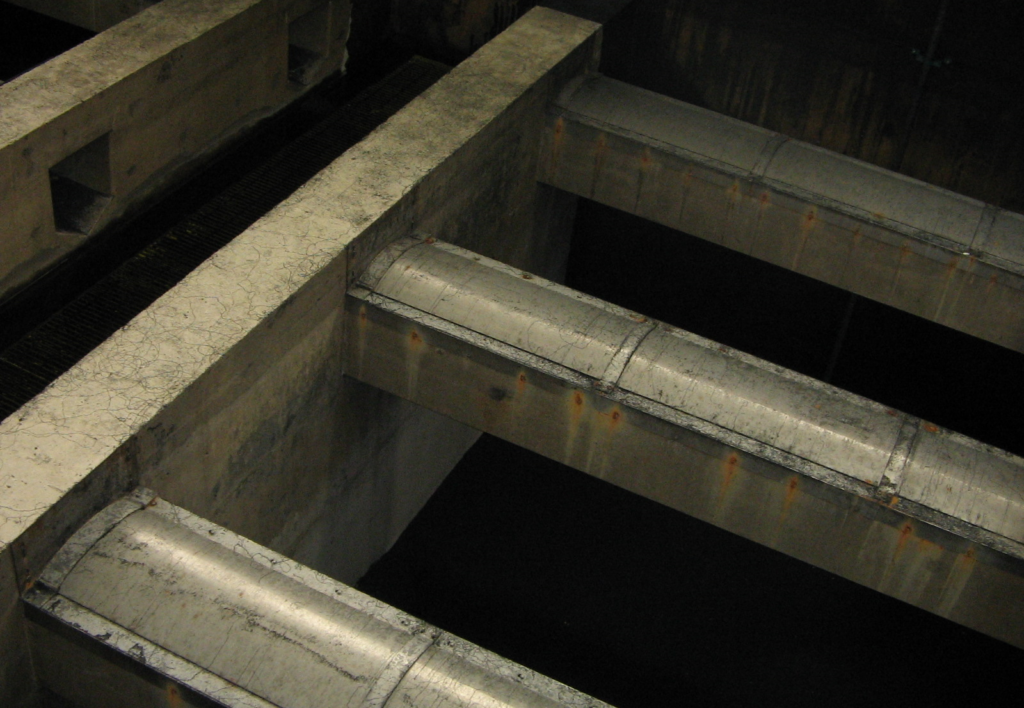
Disinfection
Process water leaving Physical Advanced Treatment enters a disinfection process prior to discharge. Disinfection creates the final barrier to pathogens. UOSA uses a chlorination and dechlorination process. Sodium hypochlorite and sodium bisulfite are used for the disinfection process.
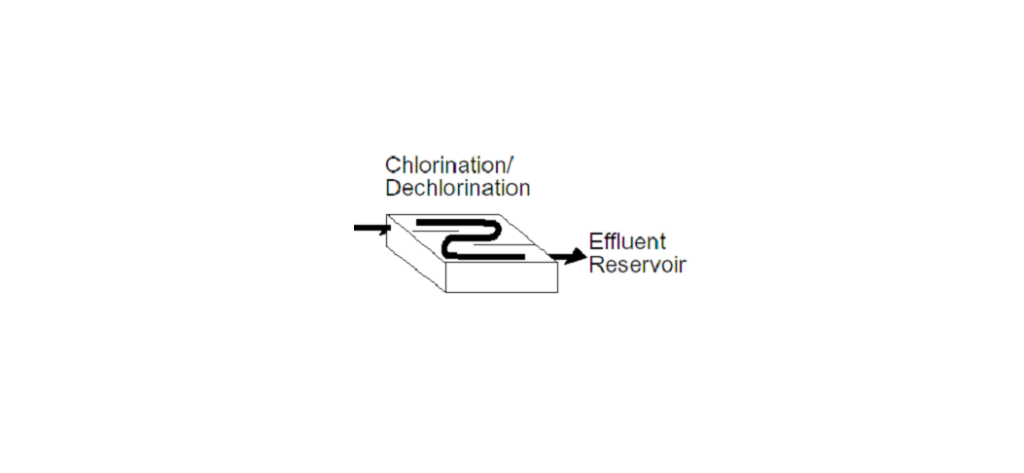
- Bulk storage of 36,000 gallons of sodium hypochlorite
- Three primary disinfection chlorination pumps and three backups (52 gph)
- Two mix chambers and four 345,000-gallon labyrinth contact basins
- Continuous online measurement of Total and free residual chlorine at mix chamber, and after 30-minute contact time
- Bulk storage of 20,000 gallons of sodium bisulfite and transfer pumps for day tanks
- Three bisulfite feed pumps (52 gph)
- Continuous online measurement of pre-dechlorination total chlorine residual for bisulfite pacing
- Continuous online measurement of post-dechlorination total chlorine residual
- Outfall to 180-million-gallon final effluent reservoir
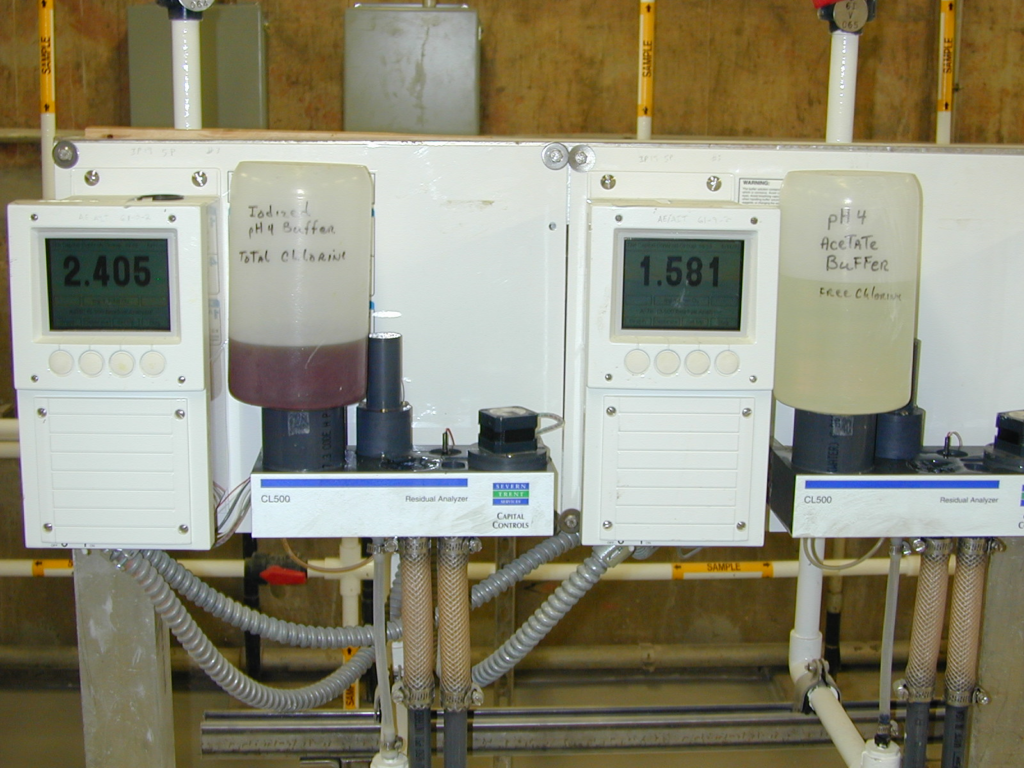
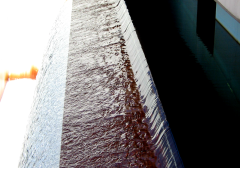
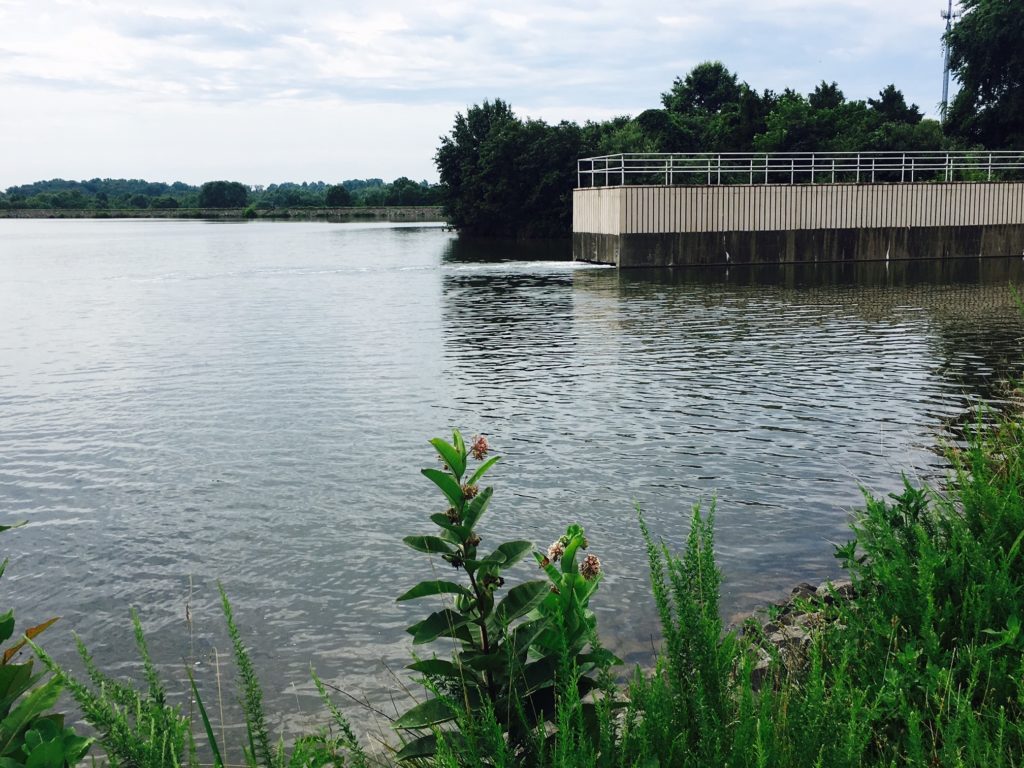
Digestion and Sludge Handling
Organic sludges from the Conventional Treatment processes are stabilized into a biosolids product used as a soil amendment and chemical fertilizer alternative. Primary sludge and waste activated sludge are screened, digested, blended, dewatered, and ultimately dried to produce fertilizer pellets.
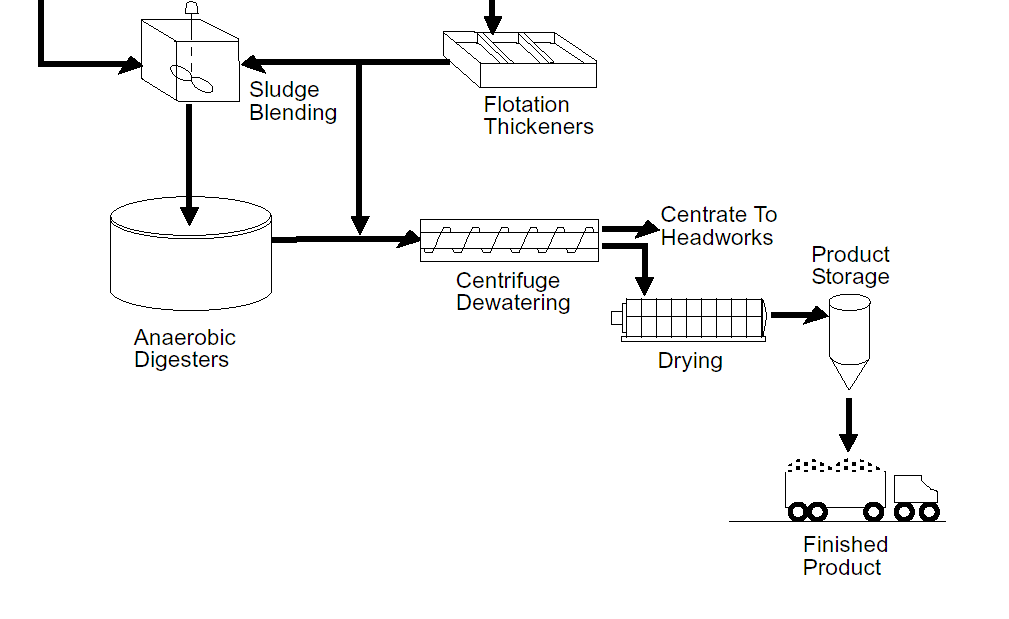
- Parkson strain presses remove particulates greater than 5 mm from primary sludge and WAS
- Dissolved air floatation thickeners and Westfalia thickening centrifuges thicken WAS to 5-6 percent
- Three one-million-gallon mesophilic anaerobic digesters with IDI gas cannon mix systems
- biogas is burned for digester heating, steam for carbon regeneration and facility heating
- exhaust gasses are captured and used as primary acid to adjust pH after high-lime process
- Blending and storage tanks (260,000 gallons) with mix and transfer pumps
- Sharples and Westfalia dewatering centrifuges
- Berlie and Andritz pelletizer systems
- rotary drum dryers
- 800 tons of pellet storage
- RDP lime stabilization system as backup
- High-quality fertilizer product
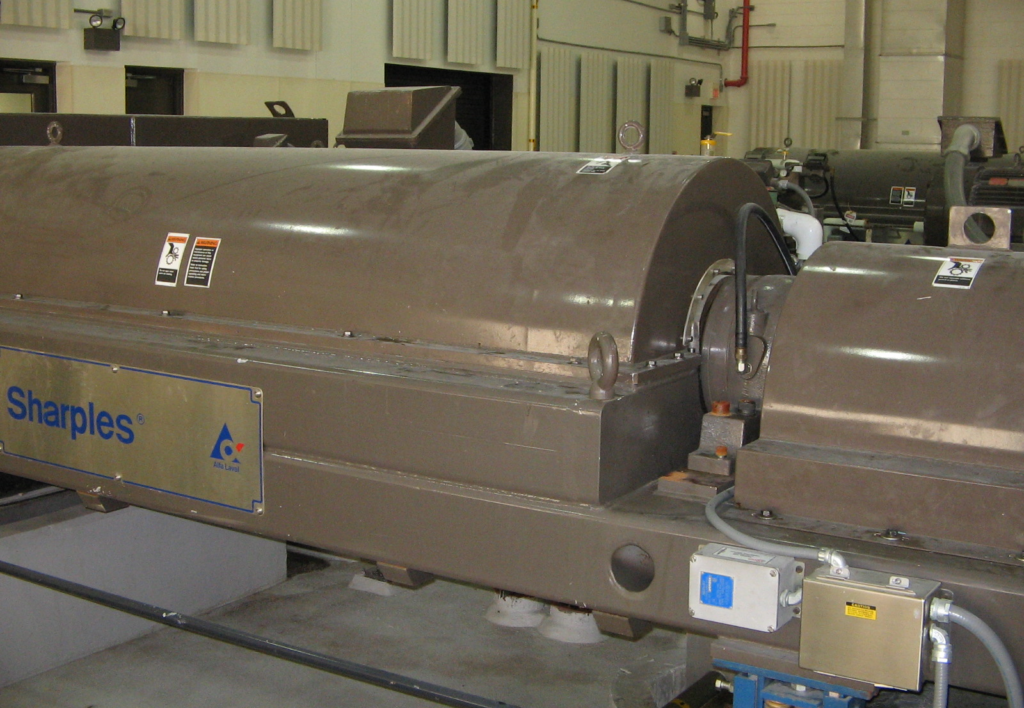
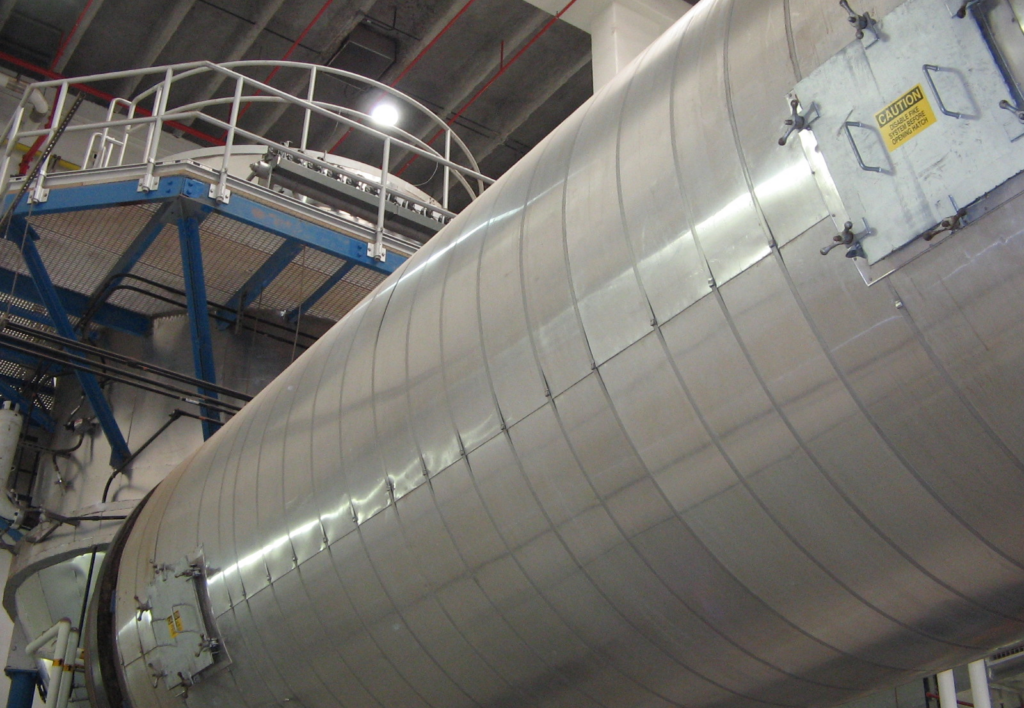
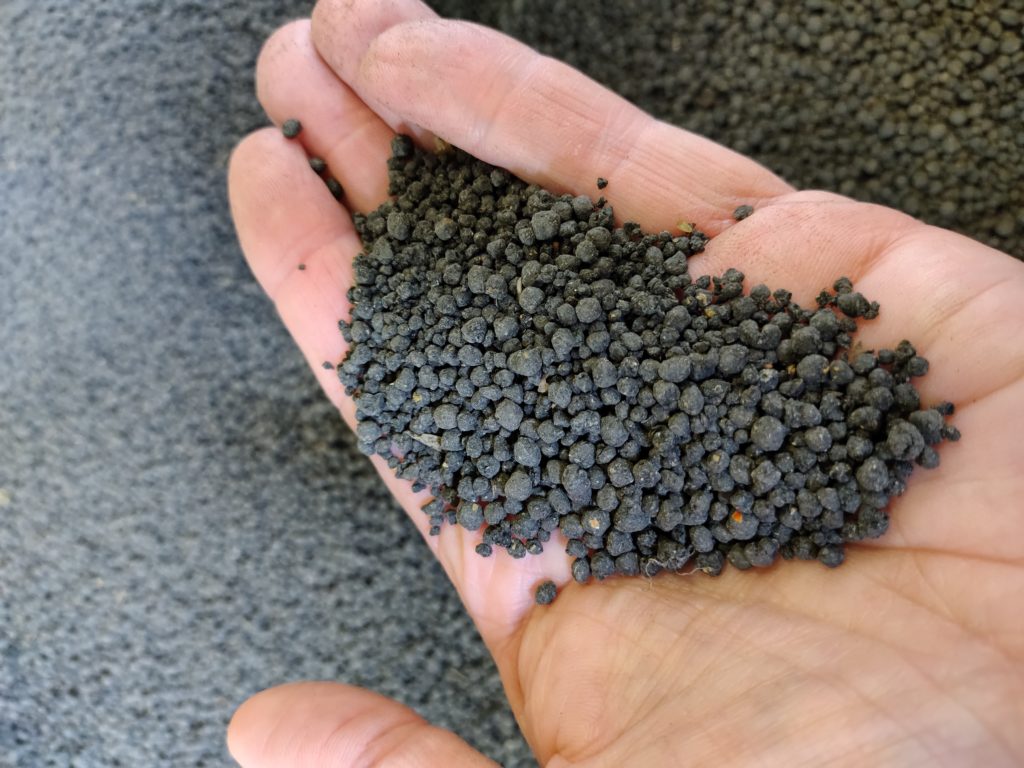